Lean Construction
Lean Construction is a management system that aims to maximize value and reduce project losses. That is, Lean Construction aims to better meet customer needs while using less of everything.
This philosophy is considered a revolution within the construction sector, since the traditional construction method is one of the industries with the worst performance in terms of the use of resources, reliability in deadlines, pollution, quality control and safety. labor.
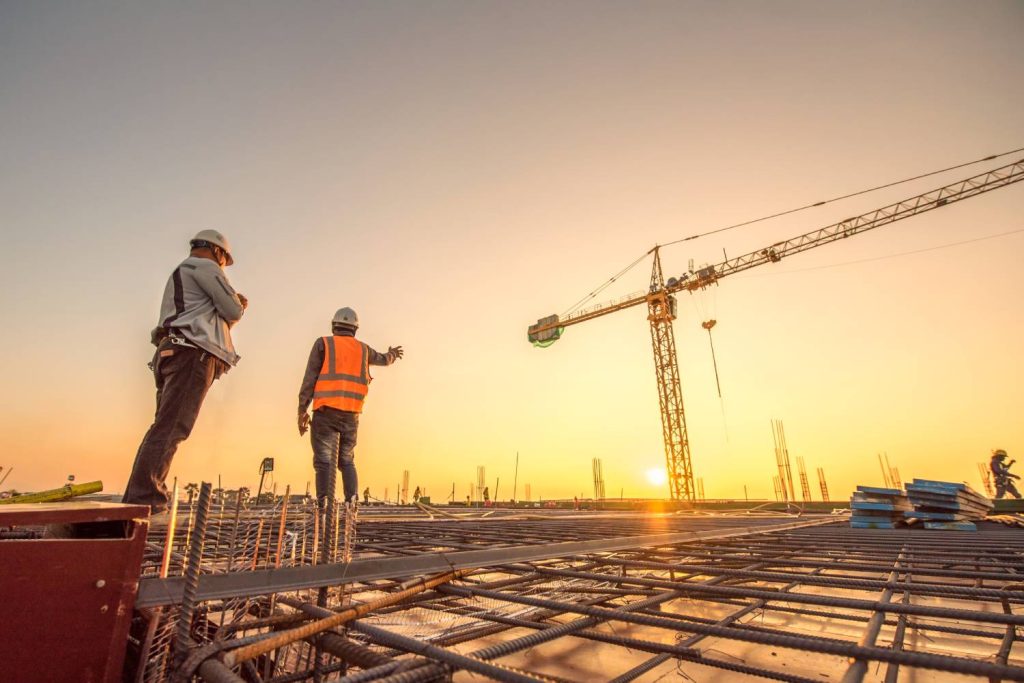
The principles on which the Lean methodology is based are the following:
- Identify the value chain map for each service or product: By creating a value stream map, we can know which activities add value to the sequence.
- Create a value stream to achieve a continuous and fluid process: Each step must add value to the other, removing obstacles from the process.
- Allow a PULL production process: Once the flow is made, it must be produced by customer orders with the exact quantity necessary to avoid unnecessary stock.
- Achieve a Continuous Improvement process: In order to optimize production cycles by making processes shorter and more efficient, obtain good production and focus efforts on customer value.
Origins of Lean Construction: The Lean Production
Around the 1950s, Toyota was a small automobile manufacturer in Japan, a country just beginning to recover from the effects of World War II. In contrast, the industry in the United States seemed unaffected by the damage of the war.
The Toyoda family (Toyoda Automatic Loom Factory, which today is still part of the Toyota conglomerate) realizes the enormous difference in productivity between their plants and North American car manufacturers, so they decide to investigate the processes in North America. and commission one of your engineers, Taiichi Ohno the objective of increasing the productivity of its plant 10 times in a period of 3 years.
The company had to adapt to produce a wide variety of automobiles in small quantities at competitive costs, disrupting the conventional logic of mass production. He found ways to combine the advantages of small batch production with economies of scale in supply and manufacturing, such as recognizing zero-waste inventories, which is where what we know as the Toyota Production System and its fundamental roots were born. of the philosophy of Lean Production.
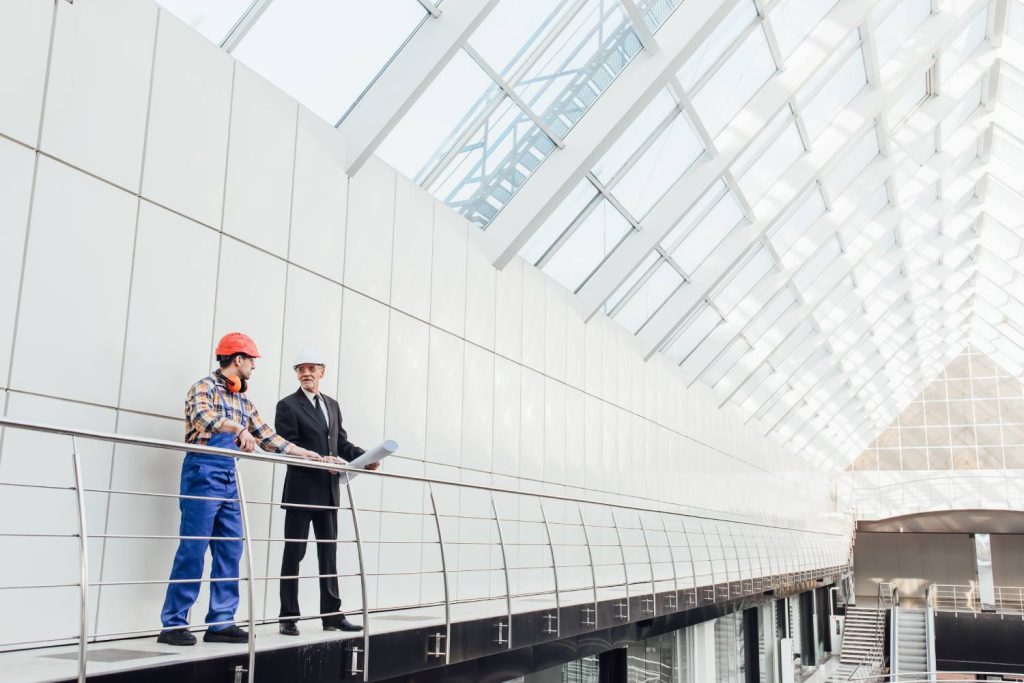
Thus, Lean is a collective term that describes a philosophy (it is not a technique, it is a process or a series of tools). Lean is a collaborative process to improve predictability in design and construction.
“Lean” from the English “lean”, is attributed to the research team that named it this way due to the focus on eliminating waste in the processes.
To be Lean, a company must:
- Be customer focused.
- Deliver Value and quality.
- Be able to identify and eliminate waste in each process you execute.
- Strive for business excellence through continuous improvements.
The process Lean construction closely related to the agile methodologies that accompany the BIM methodology.
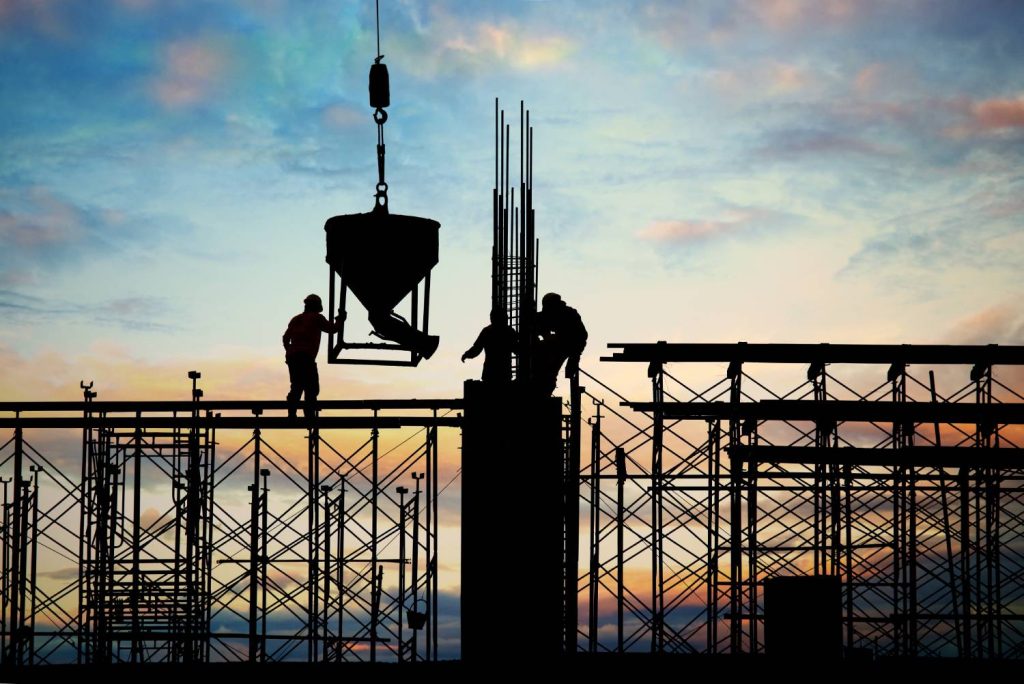
The stages of a project that is developed under the methodology BIM, following the parameters of Lean Construction from the beginning, are capable of obtaining high overall performance, being able to optimize the use of economic, material and labor resources. Allowing highly efficient Planning that allows the management of a project to be improved as the development of a work is continually evaluated.
If you want to learn how to generate highly efficient construction projects, knowing the latest technologies implemented in Buildings, do not hesitate to sign up for our Professional master in BIM and efficient Energy management.